Автомобильный завод Nissan в Санкт-Петербурге. На шаг впереди всех
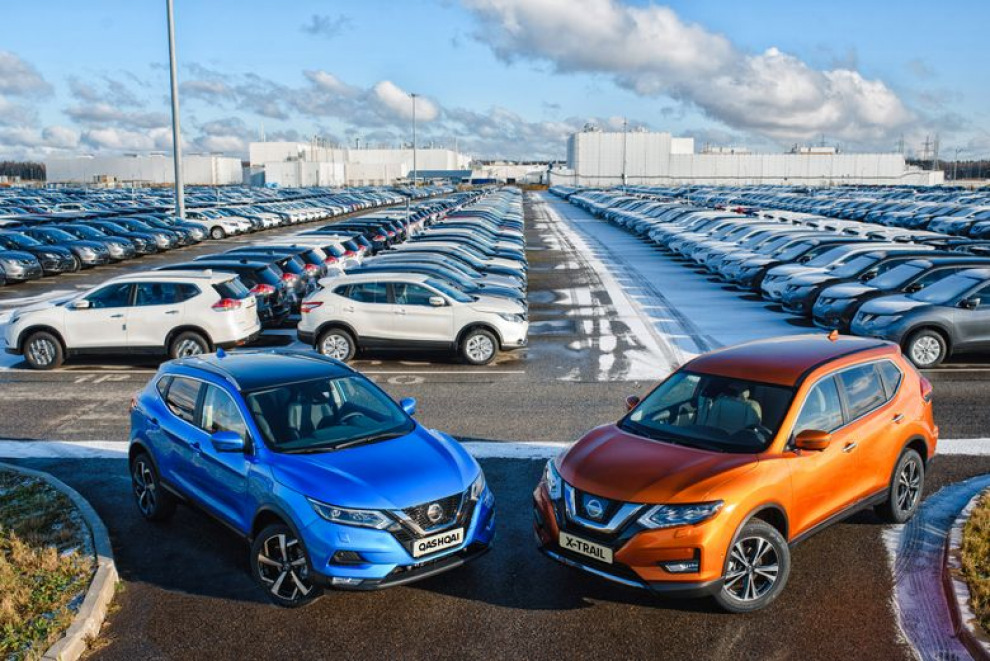
- Технологии
- 4 апреля 2019
В сознании нашего человека автозавод это что-то брутальное, с высоченными трубами, огромное и перепачканное мазутом. Это километры бетонных стен и конвейеров, армии людей в касках и горы разнообразного железа. А порой и вовсе – «проклятое место», как в знаменитом анекдоте про ВАЗ.
На заводе Nissan в Санкт-Петербурге, где совсем недавно стартовало производство новой модели Qashqai всё по-другому. Здесь светло, чисто и до автоматизма чётко. Это самое молодое предприятие в европейской производственной семье марки, оно соответствует всем передовым технологическим стандартам отрасли, требующей широкой интеграции цифровых технологий и автоматизации на всех стадиях производства. Красивые слова, да? Что стоит за ними на самом деле? Я не буду подробно описывать то, как устроен и чем занят завод. Расскажем только о самых удивительных и непривычных его достижениях.
Разумеется, в цехах работают видеокамеры. Это не редкость – так бывает часто. А вот дальше… кроме системы видеонаблюдения, есть ещё внутренняя, самостоятельная сеть обмена данными между станками, механизмами, вплоть до последнего датчика и колёсика. Всё оборудование завода объединено в систему, которая отслеживает корректность работы предприятия. Объём данных в ней настолько масштабен, что вынудил местных компьютерщиков организовать отдельный закрытый Wi-Fi исключительно для этих потребностей. Что это даёт?
Разумеется, все процедуры производства и сборки подотчётны. Помимо этого, большую часть подсобранных деталей перевозят по заводу тележки-роботы, из которых порой составляют целые роботопоезда. Так вот, даже колёса этих тележек имеют датчики, отсылающие в центральный «мозг» информацию о своём состоянии.
В результате - стопроцентная уверенность в том, что ерундовая поломка не остановит конвейер, а кроме того – оптимизация расходов на ремонт и содержание внутризаводского оборудования. Если датчик сигналит, что колесо начинает греться или буксовать, тележку отправляют в ремонт не дожидаясь поломки. Одновременно с сигналом готовится к замене и ремонтная база, где уже подбирают необходимую запчасть. Колесо тележки – деталь пустяковая, но примерно по такому же принципу мониторят работу станков, всего сложного оборудования, готовя загодя изнашиваемые детали и поддерживая высокую надёжность и точность производства в любой момент.
Кстати о точности. Отдельный цех завода работает над геометрией кузовов, непрерывно выявляя огрехи штампов или сварки. Из каждой партии деталей отбирают подопытного, на примере которого исследуют отклонения и тут же их нивелируют. Это даёт постоянно высокое качество сборки автомобилей и экономит ресурс на финишной доводке.
Завод – не завод без людей. И если в перевозке деталей они почти не задействованы, то в самом производстве – сполна. Увы, люди не роботы, им свойственно ошибаться. Система компьютерного управления участками автоматически контролирует соблюдение стандартов документации, анализирует и предоставляет статистку, отслеживает показатели работы смены. Все записи, замечания и предложения можно вносить онлайн посредством рабочих планшетов, не тратя время на составление бумажной документации. Фотография любой неприятности тоже легко и быстро помогает решать проблемы на месте.
Но и сами компьютеры не дремлют. Например, с помощью специальных алгоритмов компьютер анализирует изображения колёс и сравнивает их со спецификацией автомобиля. Такая технология применена на автоматизированном роликовом стенде проверки колёсных дисков. Ремонтная база завода также максимально современна. Вспомогательные приспособления из новейших полимерных материалов изготавливают здесь же, на 3D принтере. Это – прямая экономия средств на закупке оборудования у сторонних производителей. И даже о мелочах наподобие освещения не забыли. Здесь применяют современные источники света и централизованную систему управления потреблением ресурсов. В 80% осветительных приборов в цехах использованы экономичные светодиодные лампы. Потребление электроэнергии, газа, воды и сжатого воздуха отслеживается по 500 точкам почасового контроля.
Главный контролёр любого автомобиля не работает на заводе, он либо готов заплатить за машину в автосалоне, либо идёт к конкуренту. Поэтому отдельный департамент предприятия занят повышением удовлетворенности клиентов. Для этого создана зона установки дополнительного оборудования прямо на заводе. В результате стоимость установки аксессуаров получается ниже, чем в дилерских центрах, качество выше и не возникает никаких вопросов с гарантией. При этом, работы проводят с применением всех стандартных процессов проверки качества, внедрённых на заводе. Заводское допоборудование с 2017 года устанавливают на Nissan X-Trail и Qashqai и первым таким проектом стала защита картера. С 2018 года на этом участке налажена установка системы Яндекс.Авто на модели X-Trail и Qashqai.
В 2018 году завод Nissan в Санкт-Петербурге поставил производственный рекорд, выпустив 56 525 автомобилей. Это максимальный объём за всё время производства автомобилей Nissan в России, превышающий результаты 2017 года на 23%. Для этого созданы все условия, а всего с момента запуска в июне 2009 года и по январь 2019 года с конвейера завода в Санкт-Петербурге сошли 357 602 автомобиля. В июне 2019 года российское предприятие Nissan готовится отметить 10-летний юбилей производства, а многие новаторские идеи, реализованные на заводе копируют на Европейских производствах концерна, и это тоже впервые за всю новейшую историю отечественного автомобильного производства.